Fondation Louis Vuitton - Frank Gehry
- Ayush Mishra
- Dec 20, 2022
- 7 min read
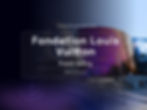
Project Specifications:
Location: | D'Acclimatation Jardin, Paris, France |
Studio: | Gehry Partners LLP |
Design: | Frank Gehry |
Built in: | 2014 |
Area: | 11,700 Sqm |
Category: | Office Space |
Photographs: | Iwan Baan , Todd Eberle |

The Louis Vuitton Foundation is a cultural center and art museum located in the Bois de Boulogne area of Paris, France, with a view of the Jardin d'Acclimatation. It was designed by architect Frank Gehry and opened to the public in October 2014 after being under construction for six years.
The Louis Vuitton Foundation museum, with a cost of $143 million, was commissioned by Bernard Arnault, CEO and chairman of the foundation's parent company, LVMH (Moët Hennessey Louis Vuitton). The idea for the museum building was developed when Arnault and architect Frank Gehry met in 2001, and the project was officially announced in 2006. Construction on the foundation, located on a 1-hectare plot of public land under a long-term lease that expires in 2062, began in March 2008.
Frank Gehry, the architect of the Louis Vuitton Foundation museum, successfully created a design that effectively communicates the client's dedication to art and culture through 21st century architecture. The building consists of a series of white blocks, referred to as "the icebergs," covered in fiber-reinforced concrete panels and surrounded by 12 large glass "sails" supported by wooden beams. The sails give the museum a transparent and dynamic appearance, while the modular design of the auditorium allows for a range of unique experiences and artistic encounters for visitors.

"A Dream Come True" by Bernard Arnault
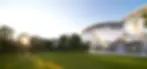
Design Philosophy :
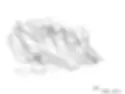
Frank Gehry, known for incorporating maritime themes in his designs, has brought the fluidity of sails to life in the facades of the IAC building in New York and the Louis Vuitton Foundation. For the foundation, he drew inspiration from the sails of ships from the late 19th and early 20th centuries, particularly the Susanne yacht built in 1911, and translated their graceful curves into rigid glass and metal. The resulting structure is a 9,000 square meter iceberg, enveloped in shimmering glass sails that seem to billow in the wind.
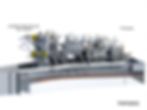


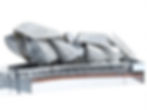
Frank Gehry's design process begins with a series of sketches that he calls "doodles," which are born out of his observations and the free flow of his hand across the page. These doodles are a combination of solid lines, circles, curves, swirls, and meanders that come together to reveal the underlying concept. The sketches for the Louis Vuitton Foundation, from the very beginning, capture the dynamic energy of a boat sailing through the wind. However, these sketches are open to interpretation and are not fully fleshed out until the design process continues.
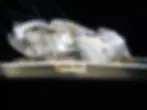
Material & Façade :
The Louis Vuitton Foundation building is composed of three blocks, each with its own unique construction logic. The primary structure is made of reinforced concrete and steel, while the secondary structure is crafted from wood and glass-coated steel.

Primary structure:
The western section of the Fondation Louis Vuitton features a solid structure made of aramid concrete beams and joists, while the central block rising above the reception hall is supported by massive steel struts. The eastern block boasts a core of reinforced concrete and iron struts. The blocks are supported by a thick 260cm concrete slab, which ensures the building's stability and uniformly distributes the weight of the glass candles. To speed up construction, the slab was laid before the candle distribution studies were completed.
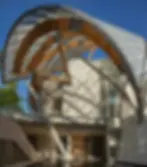
Secondary structure:
The secondary structure of the Fondation Louis Vuitton is a metal frame upon which the building's undulating facades are mounted. The facades feature tripods that support the 12 glass candles. The white coating is attached to an aluminum casing that encloses the steel structure, and the surface of the wooden frame and steel plates are angled to follow the fluid lines of the facades.

Wood frame and steel:
The tremendous weight of glass candle is supported by a mixed wood frame and steel, two materials with very different properties. Anchored to the building structure tripods, 179 beams whose length varies between 3 and 25m, with different angles from 0º to 250º placed. These steel beams wooden beams are joined by bolts. To position the larger beams crane that lifted and then were fixed in position by specialists was used. Each candle has a code: REU is the largest, covering 3,000m2 and rises 25m above the highest terrace, SHU is located below the above, it is supported by beams 179 and expands 1.700m2.
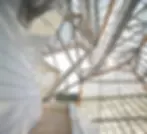
Facades :
The immense weight of the glass candles is supported by a combination of wood and steel beams, two materials with very different properties. The candles are anchored to the building structure with 179 tripods, whose lengths range from 3 to 25 meters and are angled from 0 to 250 degrees. The steel beams are connected to the wooden beams with bolts, and the larger beams were lifted into place by cranes and secured by specialists. Each candle has its own code: REU is the largest, covering 3,000 square meters and rising 25 meters above the highest terrace, while SHU is located below and spans 1,700 square meters, supported by 179 beams.

The construction :
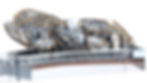
The Louis Vuitton Foundation was primarily built with reinforced concrete panels, white concrete, steel, laminated glass, and wood. The foundation slab required 11,000 cubic meters of reinforced concrete and 12 tons of steel. The 12 candles on the deck, covering a total area of 13,500 square meters, are supported by a structure of steel beams and laminated larch wood in natural tones, connected by approximately 400 stainless steel bolts. These elements join the steel beams together to create a sturdy and elegant structure.
Twelve glass sails, with a combined surface area of 13,400 square meters, float above the Louis Vuitton Foundation's "Iceberg," creating a series of complex, porous, and ever-changing spaces. While these sails do not enclose the building, they protect the terraces in inclement weather and reduce solar gain. The sails are made up of a Duplex stainless steel mesh supported by steel and glulam beams, which are themselves held in place by 179 posts. These beams are curved and sometimes twisted, and the 3,600 curved panes of glass that cover the sails are all unique, thanks to a new industrial process that allows for infinite variation in hot bending. Despite the intricate structural interweaving, there is not a single element out of place and each piece is perfectly sized.
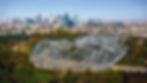

Throughout the construction process, the team working on the Louis Vuitton Foundation faced numerous technical challenges and found innovative solutions to bring Frank Gehry's design to life. From the initial conception of the project to its final touches, the team had to think outside the box to overcome these challenges, particularly when it came to the production of the glass. In order to meet the designer's specifications for curves and projections, a special furnace was created. This allowed the team to push the boundaries of their expertise and bring Gehry's vision to fruition.

Glass panels candle
The 3,600 glazed panels that make up the sails of the Louis Vuitton Foundation each have their own radius, curvature, and orientation angle, making them difficult to produce on an industrial scale. To overcome this challenge, the team turned to a hot bending mold, a technique recently developed for mass producing automotive windows. However, the machines used for this process are only capable of producing cylindrical shapes, so the team had to find the closest approximation of the desired final shape for each panel by using cylindrical molds.

To streamline the production process and ensure continuity between the panels, Gehry's Technology Study team developed software that could automate the calculation of the radius of curvature for each double glass panel. This software also calculated the mechanical strength of the panels using specialized routines, saving time and effort. It took 17 months to assemble the frame and secure the panels in place. Because the 12 glass candles overlap, the assembly process had to be highly coordinated and could not be done in isolation. In some cases, technical specialists had to be hired to work on the surface using ropes and harnesses.
White concrete panels
The walls of the Louis Vuitton Foundation's "Iceberg" are coated with Ductal white plates, which are fixed to an aluminum frame. The surface to be covered is divided into 19,072 individual rectangles, each with its own unique curvature to fit its specific position on the surface. This material is made of a mixture of high-performance concrete and metal or synthetic particles (in this case, polyester) and a small amount of water. The plates were given their white color by mixing in titanium oxide and were fitted with 1,700 metal attachments.
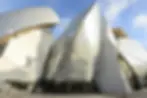
The lobby floor of the Louis Vuitton Foundation is paved with Burgundy stones and the handrails are made of steel tubes with tempered glass panels to protect the stairs. Rainwater that falls on the sails or terraces is collected and filtered in tanks to be used for cleaning the facades and roofs, watering plants, and filling sinks. Frank Gehry's innovative design required constant technical innovation throughout the construction process. From the very beginning, all partners involved in the project used Digital Project, a software program developed by Gehry Technologies based on Dassault Systèmes' Catia program, to create the complex shapes imagined by Gehry and ensure close collaboration between the various teams working on the project with a shared 3D model.
The construction of the Louis Vuitton Foundation building is in line with the LVMH Group's commitment to sustainable development. The project took into account the local flora and fauna, water tables, and the potential acoustic and human impact. The principles of sustainable development were at the heart of every stage of the project, from design to construction and future use. Once the building is open, the conservation of its natural resources will remain a priority. For example, rainwater will be collected and used for non-drinking purposes such as cleaning the building's facades and glass roofs and watering plants and terraces. This will help to minimize the consumption of drinking water in the building and ensure that it is used efficiently
Drawings :

Sustainable Practices :
The Louis Vuitton Foundation project has set a new standard for the use of advanced digital and fabrication technologies in the design and construction industry, and has served as a catalyst for innovation on a global scale. Over 400 people contributed design models, engineering rules, and assembly constraints to a common, web-hosted 3D digital model that could adapt intelligently to design requirements. More than 3,600 glass panels and 19,000 concrete panels that make up the facade were simulated using mathematical techniques and molded using advanced industrial robots, all automated from the shared 3D model. Special software was developed specifically to facilitate collaboration and work with the complex design.
The glass roof structure of the building allows it to collect and reuse rainwater and improves its geothermal power. The Foundation has also achieved its goal of obtaining HQE (Haute Qualité Environnementale) certification, which is considered to be equivalent to LEED Gold. This high level of certification was achieved through various measures to ensure environmental sustainability.